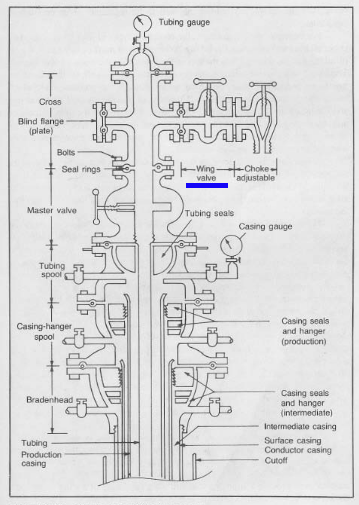
Vanne de production : Le gardien de la production pétrolière et gazière
Dans le monde complexe de l'extraction pétrolière et gazière, chaque composant joue un rôle crucial. Parmi ceux-ci, la **vanne de production** se distingue comme un gardien silencieux, régulant le flux des fluides produits du puits vers les installations de traitement.
Le cœur du puits :
Située sur l'**arbre de Noël**, l'assemblage du puits qui contrôle le flux de pétrole, de gaz et d'eau provenant du puits, la vanne de production agit comme un gardien crucial. Elle est positionnée sur le croisillon, le centre de l'arbre de Noël, où les fluides provenant du puits convergent avant de se diriger vers le traitement.
Fonction et importance :
La vanne de production est responsable de :
- Contrôle du flux : Elle agit comme une **vanne d'arrêt**, permettant à l'opérateur d'isoler complètement le puits en cas d'urgence ou de maintenance planifiée.
- Régulation du débit : La vanne peut être ouverte ou fermée partiellement pour contrôler le volume des fluides produits quittant le puits. Ceci est vital pour optimiser la production et minimiser les fluctuations de pression.
- Direction du flux : Dans certaines configurations, une vanne de production peut être utilisée pour dévier le flux de fluides vers des lignes de traitement spécifiques, permettant un traitement sélectif des différents composants.
Types et conceptions :
Les vannes de production sont généralement construites à partir de matériaux résistants aux environnements difficiles et aux fluides corrosifs, tels que l'acier inoxydable ou les alliages de haute qualité. Ils sont disponibles dans diverses conceptions, notamment :
- Vannes à soupape : Simples et fiables, ces vannes offrent une fermeture complète avec une soupape coulissante qui bloque le flux.
- Vannes à bille : Ces vannes utilisent une bille sphérique avec un trou pour contrôler le flux. Elles offrent une ouverture et une fermeture rapides et conviennent aux applications haute pression.
- Vannes à clapet : Ces vannes utilisent un clapet cylindrique avec un trou pour contrôler le flux. Elles sont souvent utilisées pour les applications à haute température.
Essentiel pour la sécurité et l'optimisation :
La vanne de production est un composant essentiel d'un système de puits, assurant :
- Sécurité : En permettant l'isolement du puits, la vanne minimise le risque de fuites incontrôlées de fluides et de dangers potentiels.
- Efficacité opérationnelle : En contrôlant les débits et en dirigeant les fluides vers des lignes de traitement spécifiques, la vanne contribue à optimiser la production et à garantir des opérations fluides.
Conclusion :
La vanne de production est un composant essentiel de l'industrie pétrolière et gazière, jouant un rôle vital dans le contrôle et la direction du flux des fluides produits. Sa construction robuste, ses conceptions polyvalentes et sa fonction essentielle en font un élément indispensable pour une production pétrolière et gazière sûre, efficace et optimisée.
Test Your Knowledge
Production Wing Valve Quiz
Instructions: Choose the best answer for each question.
1. What is the primary function of a Production Wing Valve?
a) To control the flow of fluids from the wellhead to processing facilities. b) To pump fluids from the well to the surface. c) To measure the volume of produced fluids. d) To separate oil, gas, and water.
Answer
a) To control the flow of fluids from the wellhead to processing facilities.
2. Where is the Production Wing Valve typically located?
a) At the bottom of the well. b) In the processing facility. c) On the Christmas tree. d) In the pipeline.
Answer
c) On the Christmas tree.
3. Which of the following is NOT a type of Production Wing Valve?
a) Gate Valve b) Ball Valve c) Plug Valve d) Check Valve
Answer
d) Check Valve
4. What is the main safety benefit of a Production Wing Valve?
a) It prevents leaks in the wellhead assembly. b) It allows for isolation of the well in case of emergencies. c) It reduces the risk of explosions. d) It protects workers from harmful chemicals.
Answer
b) It allows for isolation of the well in case of emergencies.
5. How does a Production Wing Valve contribute to operational efficiency?
a) By increasing the volume of fluids produced. b) By controlling flow rates and directing fluids to specific processing lines. c) By reducing the cost of production. d) By automating the wellhead operation.
Answer
b) By controlling flow rates and directing fluids to specific processing lines.
Production Wing Valve Exercise
Scenario: You are working on an oil rig and need to shut down a well for maintenance. The Production Wing Valve on the Christmas tree is a gate valve.
Task: Describe the steps involved in using the gate valve to shut down the well. Include any safety precautions you would take.
Exercice Correction
Here are the steps involved in shutting down a well using a gate valve:
- Safety First:
- Ensure all personnel are aware of the shutdown procedure.
- Confirm that the wellhead is isolated from the pipeline and processing facilities.
- Wear appropriate personal protective equipment (PPE) for the task, including safety glasses, gloves, and hard hat.
- Locate and Inspect the Valve:
- Identify the Production Wing Valve on the Christmas tree.
- Inspect the valve for any visible damage or leaks.
- Open the Valve Handwheel Slowly:
- If the valve is currently open, slowly rotate the handwheel to close the valve.
- Observe the flow rate as you close the valve to monitor for any unusual behavior.
- Close the Valve Completely:
- Continue rotating the handwheel until the valve is fully closed.
- Ensure the valve is securely closed and that the handwheel is locked in place.
- Confirm Shutdown:
- Observe the flow meters and pressure gauges to confirm that the well is completely shut down.
- Check for any leaks around the valve or in the wellhead assembly.
- Document the Shutdown:
- Record the time and date of the shutdown.
- Note any observations or issues encountered during the process.
Safety Precautions:
- Never attempt to operate a valve if you are unsure of the procedure or if there are any safety concerns.
- Always wear appropriate PPE and follow safety regulations.
- Ensure proper communication and coordination with other personnel.
- Be aware of potential hazards like high pressure, moving parts, and corrosive fluids.
Books
- "Wellhead Equipment and Operations" by John L. Bradley: Provides a comprehensive overview of wellhead equipment, including detailed explanations of valves and their functions.
- "Oil and Gas Production Operations: A Practical Approach" by Michael C. Smith: Includes sections on wellhead design, components, and valve selection for optimal performance.
- "Petroleum Engineering Handbook" edited by Donald R. Woods and George D. Hobson: A vast resource covering all aspects of oil and gas production, with dedicated chapters on wellhead systems and valve technologies.
Articles
- "Wellhead Systems and Equipment" by The American Petroleum Institute (API): A detailed guide on wellhead design, components, and regulations, including information on Production Wing Valves.
- "Production Wing Valve Selection and Maintenance" by Oil and Gas Journal: Discusses key considerations for choosing and maintaining Production Wing Valves, emphasizing safety and performance.
- "Advances in Wellhead Technology" by SPE Journal: Highlights recent developments in wellhead design and valve technologies, including improvements in reliability and automation.
Online Resources
- API (American Petroleum Institute): Their website features technical standards, publications, and resources related to oil and gas production, including information on wellhead equipment.
- SPE (Society of Petroleum Engineers): Provides a wealth of research articles, technical papers, and publications on wellhead design, valve technologies, and production optimization.
- Oil & Gas Journal: Offers industry news, technical articles, and market insights on various aspects of oil and gas operations, including wellhead equipment and valve systems.
Search Tips
- Use specific keywords: "Production Wing Valve", "Wellhead Valve", "Christmas Tree Valve", "Flow Control Valve", "Oil and Gas Valve".
- Combine keywords with specifications: "Production Wing Valve stainless steel", "Ball Valve wellhead", "Gate Valve oil production", "High Pressure Valve wellhead".
- Filter by publication date: To find recent articles and developments, use the "Past Year" filter in Google Scholar.
- Use quotes: Enclose keywords in quotation marks to search for exact phrases, e.g., "Production Wing Valve".
Techniques
Chapter 1: Techniques
1.1 Valve Operation and Control
Production Wing Valves are typically operated manually using a handwheel or lever. However, they can also be integrated with automated control systems, such as:
- Hydraulic Actuators: These actuators use hydraulic pressure to open and close the valve, allowing for remote control and precise flow regulation.
- Pneumatic Actuators: Similar to hydraulic actuators, these use compressed air to operate the valve.
- Electric Actuators: These actuators utilize electric motors to provide controlled valve actuation.
1.2 Valve Sizing and Selection
Choosing the right Production Wing Valve for a specific application involves considering factors such as:
- Flow Rate: The valve should be sized to handle the expected flow rate of produced fluids.
- Pressure Rating: The valve must withstand the maximum operating pressure of the wellhead.
- Temperature Rating: The valve should be suitable for the operating temperature of the wellhead.
- Fluid Compatibility: The valve materials must be resistant to corrosion and degradation from the fluids being processed.
1.3 Valve Testing and Maintenance
Regular testing and maintenance of Production Wing Valves are crucial for safety and operational reliability. These include:
- Leak Testing: Checking for leaks in the valve body, seals, and actuator components.
- Pressure Testing: Verifying the valve's ability to withstand its rated pressure.
- Functional Testing: Ensuring the valve opens and closes smoothly and operates as intended.
- Lubrication: Regularly lubricating moving parts to prevent wear and tear.
1.4 Safety Considerations
Production Wing Valves are designed with safety features to prevent accidental opening or closing. These include:
- Locking Mechanisms: To prevent unauthorized operation of the valve.
- Pressure Relief Valves: To release excess pressure and prevent catastrophic failure.
- Fail-Safe Mechanisms: Designed to automatically close the valve in case of power failure or other emergencies.
Chapter 2: Models
2.1 Gate Valves
- Description: These valves utilize a sliding gate to block or allow the flow of fluids.
- Advantages: Simple design, reliable operation, low maintenance.
- Disadvantages: Slower opening and closing compared to other valve types, may not be suitable for high-pressure applications.
- Applications: Suitable for general purpose shut-off and flow regulation.
2.2 Ball Valves
- Description: These valves use a spherical ball with a hole to control fluid flow. The ball rotates to open or close the flow path.
- Advantages: Fast opening and closing, compact design, suitable for high-pressure applications.
- Disadvantages: May be more prone to wear and tear in high-cycle applications.
- Applications: Ideal for isolating and regulating fluid flow in demanding environments.
2.3 Plug Valves
- Description: These valves utilize a cylindrical plug with a hole to control fluid flow. The plug rotates to align the hole with the flow path, allowing or restricting the flow.
- Advantages: Robust construction, suitable for high-temperature applications, resistant to abrasive fluids.
- Disadvantages: More complex design, potentially higher maintenance requirements compared to gate valves.
- Applications: Commonly used for high-temperature and abrasive fluid applications.
2.4 Other Models
- Butterfly Valves: Similar to ball valves but utilize a disc-shaped element instead of a ball.
- Check Valves: Allow fluid flow in one direction only, preventing backflow.
Chapter 3: Software
3.1 Valve Control Systems
Software plays a crucial role in managing and controlling Production Wing Valves. These systems include:
- SCADA (Supervisory Control and Data Acquisition): Systems that monitor and control multiple valves and other equipment in an oil and gas production facility.
- PLC (Programmable Logic Controller): These controllers automate valve operation based on predefined logic and parameters.
- DCS (Distributed Control System): This system integrates multiple PLCs and other control elements to manage complex processes.
3.2 Valve Simulation Software
Software tools are used to simulate the behavior of Production Wing Valves in various scenarios, such as:
- Flow Modeling: To predict flow rates and pressures under different operating conditions.
- Stress Analysis: To assess the valve's structural integrity under pressure and other loads.
- Performance Optimization: To determine the optimal valve settings for efficient production.
Chapter 4: Best Practices
4.1 Valve Installation and Commissioning
- Ensure proper installation according to manufacturer specifications.
- Conduct pre-commissioning tests to verify valve functionality.
- Calibrate actuators and control systems.
4.2 Operation and Maintenance
- Follow manufacturer's operating instructions.
- Implement a regular maintenance schedule for inspection, testing, and lubrication.
- Keep detailed records of all maintenance activities.
- Train operators on proper valve operation and troubleshooting techniques.
4.3 Safety Procedures
- Implement lockout/tagout procedures to prevent accidental valve operation.
- Provide adequate personal protective equipment (PPE) for operators.
- Train operators on emergency response procedures in case of valve malfunction or leaks.
4.4 Optimization and Upgrading
- Regularly review and optimize valve performance to ensure efficient production.
- Consider upgrading to newer valve models with improved features and functionality.
Chapter 5: Case Studies
5.1 Optimizing Production Efficiency
- A case study showcasing the use of automated valve control systems to optimize flow rates and reduce production costs.
- Analyze the impact of integrating valves with SCADA systems.
5.2 Improving Safety and Reliability
- A case study demonstrating the effectiveness of fail-safe mechanisms in preventing accidents and ensuring wellhead safety.
- Examine the benefits of using high-quality valves and materials for enhanced reliability and longevity.
5.3 Addressing Environmental Concerns
- A case study illustrating how advanced valve technologies contribute to reducing emissions and environmental impact.
- Explore the use of valves with leak-tight seals and minimized maintenance requirements.
5.4 Innovative Applications
- A case study highlighting new applications of Production Wing Valves in emerging technologies, such as hydraulic fracturing or carbon capture and storage.
- Analyze the role of valves in enabling future advancements in the oil and gas industry.
Comments