KALREZ™ : Le joint haute température pour les applications pétrolières et gazières
Dans le monde exigeant de l'extraction et du traitement du pétrole et du gaz, la fiabilité est primordiale. Des plateformes de forage aux raffineries, les composants doivent résister à des températures, des pressions et des environnements corrosifs extrêmes. Un élément clé pour garantir l'intégrité opérationnelle est l'utilisation de joints robustes, et KALREZ™ se distingue comme une solution de premier plan pour les applications à haute température.
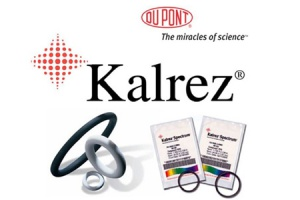
Qu'est-ce que KALREZ™ ?
KALREZ™ n'est pas seulement un joint, mais une marque détenue par DuPont™ pour un perfluoroélastomère (FFKM). Les FFKM sont des élastomères hautement spécialisés réputés pour leur exceptionnelle résistance chimique et thermique. Cela fait de KALREZ™ un matériau idéal pour les applications pétrolières et gazières exigeantes où les élastomères conventionnels peinent à performer.
Propriétés clés de KALREZ™ :
- Résistance à haute température : KALREZ™ peut fonctionner à des températures allant jusqu'à 327°C (620°F), ce qui est considérablement plus élevé que les élastomères standard. Cela le rend adapté aux environnements où des températures élevées sont rencontrées, comme le forage en profondeur, le raffinage du pétrole et le traitement du gaz.
- Résistance chimique : KALREZ™ résiste à un large éventail de produits chimiques et de solvants couramment rencontrés dans les opérations pétrolières et gazières, y compris les hydrocarbures, les acides et les bases. Cela garantit des performances durables même dans des environnements agressifs.
- Faible perméabilité : La structure moléculaire serrée de KALREZ™ le rend hautement imperméable aux gaz, empêchant les fuites et maintenant l'intégrité du système.
- Faible fluage : KALREZ™ conserve sa forme et sa fonction même après une exposition prolongée à des températures et des pressions élevées, garantissant des performances constantes au fil du temps.
Applications dans le domaine du pétrole et du gaz :
KALREZ™ est utilisé dans une variété d'applications pétrolières et gazières, notamment :
- Forage en profondeur : Étanchéité des équipements de fond de trou tels que les vannes et les pompes.
- Traitement du pétrole et du gaz : Étanchéité des pompes, compresseurs, vannes et autres équipements de traitement.
- Canalisations et transport : Étanchéité des vannes et des raccords dans les canalisations haute pression.
- Turbines à gaz et moteurs : Étanchéité des composants du moteur, y compris les roulements et les arbres.
Avantages de l'utilisation de KALREZ™ :
- Fiabilité accrue : La résistance de KALREZ™ aux conditions difficiles minimise les temps d'arrêt et les réparations coûteuses.
- Sécurité accrue : Les propriétés d'étanchéité robustes de KALREZ™ empêchent les fuites et garantissent le fonctionnement sûr des équipements.
- Durée de vie accrue : KALREZ™ peut résister à des environnements exigeants pendant de longues périodes, réduisant les besoins de maintenance et les coûts globaux.
Conclusion :
KALREZ™ représente une avancée significative dans la technologie d'étanchéité à haute température pour l'industrie pétrolière et gazière. Ses caractéristiques de performance exceptionnelles garantissent un fonctionnement fiable dans les environnements les plus exigeants, contribuant en fin de compte à des opérations plus sûres, plus efficaces et plus rentables. Alors que l'industrie continue de repousser les limites de l'innovation et de l'exploration, l'utilisation de matériaux haute performance comme KALREZ™ restera cruciale pour surmonter les défis de la production et du traitement de l'énergie.
Test Your Knowledge
KALREZ™ Quiz
Instructions: Choose the best answer for each question.
1. What type of material is KALREZ™ made of?
a) Silicone b) Nitrile c) Perfluoroelastomer (FFKM) d) Polytetrafluoroethylene (PTFE)
Answer
c) Perfluoroelastomer (FFKM)
2. What is the maximum operating temperature of KALREZ™ seals?
a) 150°C (302°F) b) 200°C (392°F) c) 250°C (482°F) d) 327°C (620°F)
Answer
d) 327°C (620°F)
3. Which of these properties is NOT a key advantage of KALREZ™ seals?
a) High temperature resistance b) Chemical resistance c) High permeability d) Low compression set
Answer
c) High permeability
4. In which of these oil and gas applications is KALREZ™ NOT typically used?
a) Downhole drilling b) Oil & Gas processing c) Pipeline and transmission d) Solar panel manufacturing
Answer
d) Solar panel manufacturing
5. What is a major benefit of using KALREZ™ seals in oil and gas operations?
a) Increased use of hazardous materials b) Reduced reliance on skilled labor c) Improved reliability and safety d) Lower initial cost compared to other seals
Answer
c) Improved reliability and safety
KALREZ™ Exercise
Scenario: You are a project engineer working on a new oil well drilling project. The well will be located in a high-pressure, high-temperature environment. You are tasked with choosing the best sealing material for downhole equipment like valves and pumps.
Task:
- Explain why KALREZ™ would be a suitable choice for this application.
- List at least three other sealing materials that could be used for downhole equipment and discuss their advantages and disadvantages compared to KALREZ™.
- Considering the harsh environment and the importance of reliable operation, provide a strong argument for using KALREZ™ over the alternatives.
Exercise Correction
1. KALREZ™ Suitability:
KALREZ™ is highly suitable for this application due to its:
- High temperature resistance: The well's high-temperature environment necessitates a material that can withstand extreme heat without degrading, which KALREZ™ excels at.
- Chemical resistance: Downhole equipment is exposed to various corrosive fluids and gases. KALREZ™ provides excellent resistance to hydrocarbons, acids, and other chemicals commonly found in oil and gas operations.
- Low permeability: Preventing leaks is crucial for downhole equipment to maintain system integrity and safety. KALREZ™'s low permeability ensures minimal gas or fluid leakage.
2. Alternative Sealing Materials:
- NBR (Nitrile Butadiene Rubber): Advantages: Lower cost than KALREZ™; good resistance to oils and fuels. Disadvantages: Limited high-temperature performance (typically up to 120°C); less resistant to chemicals than KALREZ™.
- FKM (Fluoroelastomer): Advantages: Good chemical resistance and high-temperature performance (up to 200°C); lower cost than KALREZ™. Disadvantages: Lower temperature resistance and chemical resistance compared to KALREZ™; higher permeability.
- EPDM (Ethylene Propylene Diene Monomer): Advantages: Good weather resistance; relatively low cost. Disadvantages: Limited temperature resistance (up to 150°C); not resistant to many chemicals found in oil and gas operations.
3. Argument for KALREZ&trade:
While alternatives like FKM and NBR offer some advantages, KALREZ™ stands out as the best choice for this high-pressure, high-temperature downhole application. Its superior temperature resistance, chemical resistance, and low permeability significantly enhance reliability and safety. Using KALREZ™ minimizes the risk of costly repairs, downtime, and potential environmental damage. While it may have a higher initial cost compared to other materials, its extended service life and reduced maintenance needs ultimately make it a more cost-effective and reliable solution for this demanding application.
Books
- DuPont™ KALREZ™ Perfluoroelastomer: A Guide to Selection and Application: This comprehensive guide is directly from the manufacturer, DuPont, and covers all aspects of KALREZ™, including selection, design considerations, and application data for various oil & gas applications.
Articles
- "KALREZ™ Perfluoroelastomer for Oil and Gas Applications": This article from DuPont explains the material's unique properties, its advantages in oil & gas environments, and various case studies showcasing its success.
Online Resources
- DuPont™ KALREZ™ Website: This official website provides extensive information about KALREZ™, including detailed specifications, applications, and technical support resources.
Search Tips
- "KALREZ™ oil and gas applications": This search phrase will lead you to relevant articles, case studies, and technical information specifically related to KALREZ™ use in oil & gas.
Techniques
KALREZ™: The High-Temperature Seal for Oil & Gas Applications
Chapter 1: Techniques
1.1 Sealing Techniques with KALREZ™
KALREZ™ can be incorporated into various sealing techniques to address specific needs within the oil and gas industry.
- Static Seals: For stationary applications, KALREZ™ O-rings are widely used. They offer excellent resistance to leakage and compression set, crucial for sealing valves, pumps, and other stationary equipment.
- Dynamic Seals: For moving parts like shafts and pistons, KALREZ™ can be used in various dynamic sealing configurations, such as:
- Rotary Seals: These seals employ KALREZ™ components to prevent leakage between rotating shafts and stationary housings, commonly found in pumps and compressors.
- Reciprocating Seals: These seals address the challenges of sealing reciprocating parts like pistons and rods, crucial for applications like drilling and processing equipment.
- Gaskets: KALREZ™ can be used to create flat gaskets that provide a tight seal between two mating surfaces. These gaskets are ideal for sealing flanges, housings, and other non-moving components.
1.2 Considerations for KALREZ™ Sealing Applications:
- Operating Temperature and Pressure: The extreme temperature and pressure conditions of oil and gas applications necessitate careful consideration of the specific KALREZ™ grade. DuPont offers various grades with varying temperature and pressure resistance to suit diverse needs.
- Chemical Compatibility: The presence of aggressive chemicals like hydrocarbons, acids, and bases requires selecting a KALREZ™ grade with excellent chemical resistance.
- Design and Material Compatibility: Proper design of the seal and compatible materials are crucial for optimal performance. This includes ensuring appropriate seal compression and avoiding compatibility issues with other materials used in the system.
- Maintenance and Inspection: While KALREZ™ offers exceptional longevity, regular inspection and maintenance are still necessary to ensure proper seal function and prevent potential leaks.
1.3 Advantages of KALREZ™ Sealing Techniques:
- Improved Reliability: KALREZ™ seals offer high reliability and extended service life, reducing maintenance needs and operational downtime.
- Enhanced Safety: By effectively preventing leakage, KALREZ™ seals contribute to improved safety in oil and gas operations, reducing environmental risks and safeguarding personnel.
- Increased Efficiency: Minimized leakage and downtime translate to higher operational efficiency and overall cost savings.
- Environmental Sustainability: KALREZ™ seals minimize emissions and waste associated with leakage, promoting environmental sustainability.
Chapter 2: Models
2.1 KALREZ™ Material Grades:
DuPont offers a range of KALREZ™ material grades specifically tailored for diverse oil and gas applications. These grades differ in their composition, properties, and performance characteristics.
- Standard Grades: Designed for general applications and provide a balance of chemical resistance and temperature performance.
- High-Temperature Grades: Engineered to withstand extremely high temperatures encountered in downhole drilling, refining, and processing.
- Specialty Grades: Developed for specific applications requiring enhanced chemical resistance, such as resistance to certain acids, bases, or solvents.
2.2 Determining the Right KALREZ™ Grade:
- Operating Conditions: Temperature, pressure, and the presence of specific chemicals are key factors in selecting the appropriate KALREZ™ grade.
- Application Requirements: The specific demands of the application, such as dynamic or static sealing, will also influence the grade selection.
- Performance Criteria: Factors like compression set, permeability, and long-term durability play a crucial role in determining the best KALREZ™ grade.
2.3 Key Features of Popular KALREZ™ Grades:
- KALREZ™ 1000: A general-purpose grade with excellent chemical resistance and temperature performance, suitable for various applications.
- KALREZ™ 1050: Designed for high-temperature applications, offering outstanding resistance to heat and aggressive chemicals.
- KALREZ™ 1070: A specialty grade with enhanced resistance to aggressive acids and solvents, ideal for demanding applications.
2.4 Advancements in KALREZ™ Technology:
DuPont continues to innovate and improve KALREZ™ technology, introducing new grades with enhanced performance characteristics. These advancements include:
- Improved Temperature Resistance: New grades allow for operation at even higher temperatures, expanding the application range of KALREZ™ seals.
- Enhanced Chemical Resistance: Recent developments have increased the resistance of KALREZ™ to specific chemicals, providing greater versatility.
- Improved Compression Set Resistance: New grades minimize compression set, ensuring consistent seal performance even after prolonged exposure to high temperatures and pressures.
Chapter 3: Software
3.1 Engineering Software for KALREZ™ Design and Selection:
Specialized software programs are available to assist engineers in designing and selecting KALREZ™ seals for oil and gas applications.
- Seal Design Software: These programs allow users to create and analyze various seal configurations, optimizing design parameters for optimal performance.
- Material Selection Software: These programs assist in identifying the best KALREZ™ grade based on specific application requirements, operating conditions, and performance criteria.
- Finite Element Analysis (FEA) Software: FEA software can simulate seal behavior under various conditions, providing valuable insights into stress distribution, deformation, and potential failure points.
3.2 Benefits of Using Software for KALREZ™ Applications:
- Optimized Seal Design: Software tools enable engineers to design seals that meet specific application requirements and maximize performance.
- Accurate Material Selection: Software assists in choosing the most appropriate KALREZ™ grade based on detailed operational data.
- Improved Accuracy and Efficiency: Software tools streamline the design and selection process, reducing errors and improving efficiency.
- Predictive Analysis: FEA software enables predictive analysis of seal behavior, identifying potential failure modes and improving overall reliability.
3.3 Examples of KALREZ™ Software Tools:
- DuPont's KALREZ™ Design and Selection Tool: An online platform providing comprehensive resources for designing and selecting KALREZ™ seals.
- SolidWorks, ANSYS, and ABAQUS: Popular FEA software packages used for simulating seal behavior under various load conditions.
Chapter 4: Best Practices
4.1 Best Practices for KALREZ™ Seal Design and Installation:
- Proper Seal Selection: Choose the correct KALREZ™ grade based on operating conditions, application requirements, and performance criteria.
- Appropriate Seal Design: Ensure the seal design considers factors like compression, pressure, and temperature to prevent leakage and premature failure.
- Compatible Materials: Avoid using materials that may react with or degrade KALREZ™ during operation.
- Correct Installation: Install the seal correctly to ensure proper sealing and minimize stress on the material.
- Adequate Lubrication: Use compatible lubricants to reduce friction and wear on the sealing surfaces.
- Proper Handling and Storage: Store KALREZ™ seals in a cool, dry place, protected from sunlight and excessive heat.
4.2 Best Practices for KALREZ™ Seal Maintenance and Inspection:
- Regular Inspection: Regularly inspect KALREZ™ seals for signs of wear, damage, or leakage.
- Proper Maintenance: Follow the manufacturer's recommendations for maintenance and replacement procedures.
- Accurate Record Keeping: Maintain accurate records of seal installations, inspections, and replacements to track performance and identify potential issues.
4.3 Best Practices for KALREZ™ Seal Troubleshooting:
- Identify the Problem: Determine the specific cause of leakage or failure by analyzing the seal's condition and the surrounding environment.
- Investigate Possible Causes: Consider factors like improper seal selection, installation errors, incompatible materials, excessive wear, or environmental degradation.
- Implement Corrective Actions: Take appropriate measures to address the identified cause, such as replacing the seal, adjusting the design, or modifying operating conditions.
Chapter 5: Case Studies
5.1 Case Study: Downhole Drilling Application
- Challenge: Sealing a downhole valve in a high-temperature and high-pressure drilling environment.
- Solution: A KALREZ™ O-ring was chosen for its excellent temperature resistance and chemical compatibility with drilling fluids.
- Result: The KALREZ™ seal successfully prevented leakage and ensured the safe and efficient operation of the valve, extending its service life and reducing downtime.
5.2 Case Study: Oil Refining Process
- Challenge: Sealing a pump handling hot, corrosive crude oil in a refinery setting.
- Solution: A custom KALREZ™ rotary seal was designed for this demanding application.
- Result: The KALREZ™ seal prevented leakage, minimized wear on the pump shaft, and ensured continuous operation with minimal maintenance requirements.
5.3 Case Study: Gas Turbine Engine
- Challenge: Sealing a critical bearing in a gas turbine engine operating at high temperatures and pressures.
- Solution: A KALREZ™ gasket was employed to provide a tight seal between the bearing housing and the engine casing.
- Result: The KALREZ™ gasket effectively prevented leakage, ensuring the safe and reliable operation of the gas turbine engine, reducing downtime and improving overall efficiency.
Conclusion:
KALREZ™ stands out as a reliable and durable solution for high-temperature sealing in the oil and gas industry. By utilizing proper design, installation, and maintenance practices, operators can leverage the exceptional properties of KALREZ™ to enhance safety, reliability, and efficiency in their operations. As the oil and gas industry continues to evolve, KALREZ™ will play a crucial role in tackling the challenges of energy production and processing in the most demanding environments.
Comments