جودة سوائل التحفيز الرغوية لعمليات النفط والغاز: معلمة حاسمة
تلعب سوائل التحفيز الرغوية دورًا حيويًا في تحسين إنتاج النفط والغاز من خلال تحسين كفاءة مسح الخزان وزيادة إنتاجية الآبار. تتكون هذه السوائل عادةً من مرحلة غازية ومرحلة سائلة، وتستفيد من الخصائص الفريدة للرغوة لتحقيق هذه الأهداف. واحدة من أهم المعلمات التي تحدد فعالية سائل التحفيز الرغوي هي الجودة، والتي تُقيس جزء الحجم من المرحلة الداخلية داخل الرغوة.
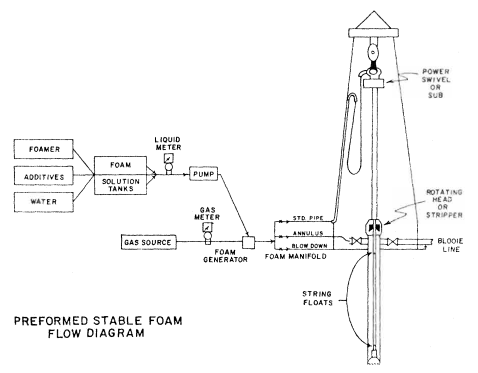
ما هي "الجودة" في سوائل التحفيز الرغوية؟
في سياق تحفيز الرغوة، تشير "الجودة" إلى نسبة حجم المرحلة الداخلية (الغاز) إلى إجمالي حجم الرغوة. توفر هذه النسبة مؤشرًا أساسيًا لاستقرار الرغوة وحركتها وأدائها بشكل عام.
لماذا تعتبر الجودة مهمة؟
- الاستقرار: تُشير رغوة ذات جودة أعلى بشكل عام إلى قدر أكبر من الاستقرار. يعني ذلك أن هيكل الرغوة يمكنه تحمل تغيرات الضغط والبقاء سليمًا لفترة أطول، مما يسمح له بإزاحة السوائل بفعالية وتحسين كفاءة مسح الخزان.
- الحركة: تؤثر الجودة على حركة الرغوة داخل الخزان. تميل الرغوة ذات جودة أقل، مع جزء غاز أصغر، إلى إظهار حركة أعلى، مما يسمح لها باختراق التكوينات الضيقة والوصول إلى المناطق الأقل وصولاً.
- الأداء: تؤثر جودة الرغوة بشكل مباشر على أدائها في تحفيز إنتاج النفط والغاز. يعد تحسين الجودة لخزان محدد وظروف بئر معينة أمرًا بالغ الأهمية لتحقيق النتائج المرجوة، مثل زيادة استخلاص النفط أو تحسين معدلات إنتاج الغاز.
العوامل التي تؤثر على جودة الرغوة:
تؤثر العديد من العوامل على جودة سائل التحفيز الرغوي، بما في ذلك:
- نوع الغاز: يؤثر نوع الغاز المستخدم (مثل النيتروجين، ثاني أكسيد الكربون) على استقرار الرغوة وجودتها.
- تركيز المادة السطحية: يلعب تركيز المادة السطحية دورًا مهمًا في استقرار هيكل الرغوة والحفاظ على جودتها.
- درجة الحرارة والضغط: يمكن أن تؤثر درجات الحرارة والضغوط المرتفعة على استقرار الرغوة، مما يؤدي إلى اختلافات في الجودة.
- خصائص الخزان: يمكن أن تؤثر خصائص الخزان، مثل النفاذية وتوزيع حجم المسام، على جودة الرغوة من خلال التأثير على حركتها وتوزيعها داخل الخزان.
قياس جودة الرغوة:
يمكن قياس جودة الرغوة باستخدام تقنيات مختلفة، مثل:
- التفتيش البصري: تتضمن هذه الطريقة مراقبة مظهر الرغوة وتحديد نسبة المرحلتين الغازية والسائلة.
- قياس انخفاض الضغط: يمكن أن يوفر قياس انخفاض الضغط عبر عمود الرغوة مؤشرًا لمقاومته للتدفق وجودته.
- معدات متخصصة: تتوفر العديد من الأدوات المتخصصة لقياس جودة الرغوة في ظروف المختبر والميدان، مما يسمح بقياسات أكثر دقة وموثوقية.
الاستنتاج:
تُعد جودة الرغوة معلمة حاسمة في تصميم وتطبيق سوائل التحفيز الرغوي في عمليات النفط والغاز. يُعد فهم العوامل التي تؤثر على الجودة واستخدام تقنيات القياس المناسبة أمرًا ضروريًا لتحسين أداء الرغوة وتحقيق أقصى قدر من كفاءة الإنتاج. من خلال التحكم الدقيق وتعديل جودة الرغوة، يمكن للمشغلين استخدام تقنيات التحفيز الرغوية بفعالية لتحسين كفاءة مسح الخزان وتعزيز استخلاص النفط والغاز.
Test Your Knowledge
Quiz: Quality in Foam Stimulation Fluids
Instructions: Choose the best answer for each question.
1. What does "quality" refer to in the context of foam stimulation fluids?
a) The strength of the surfactant used in the foam. b) The total volume of the foam generated. c) The percentage of gas in the foam's total volume. d) The pressure at which the foam is injected into the reservoir.
Answer
The correct answer is **c) The percentage of gas in the foam's total volume.**
2. Which of the following is NOT a factor affecting foam quality?
a) Type of gas used. b) Concentration of the surfactant. c) Reservoir temperature and pressure. d) The type of oil being extracted.
Answer
The correct answer is **d) The type of oil being extracted.** While oil properties can influence well productivity, they do not directly affect foam quality itself.
3. What is the main benefit of a higher quality foam in terms of reservoir sweep efficiency?
a) It allows the foam to travel further and faster in the reservoir. b) It reduces the amount of gas required for foam generation. c) It increases the viscosity of the foam, making it more effective at pushing oil. d) It ensures the foam remains stable and intact for longer periods, allowing it to displace more fluids.
Answer
The correct answer is **d) It ensures the foam remains stable and intact for longer periods, allowing it to displace more fluids.**
4. Which of the following techniques can be used to measure foam quality?
a) Visual inspection only. b) Pressure drop measurement only. c) Specialized equipment only. d) All of the above.
Answer
The correct answer is **d) All of the above.** Different methods can be used depending on the specific situation and desired level of accuracy.
5. Why is optimizing foam quality crucial for maximizing production efficiency?
a) It ensures the foam can be injected into the reservoir at the lowest possible pressure. b) It reduces the overall cost of foam generation and application. c) It maximizes the effectiveness of the foam in displacing fluids and improving reservoir sweep efficiency. d) It minimizes the risk of foam breaking down before reaching the target area.
Answer
The correct answer is **c) It maximizes the effectiveness of the foam in displacing fluids and improving reservoir sweep efficiency.** Optimizing quality ensures the foam performs its intended function efficiently, leading to higher production.
Exercise: Foam Quality and Reservoir Characteristics
Scenario: You are working on a foam stimulation project in a tight gas reservoir with low permeability and high pressure.
Task: Explain how the reservoir characteristics will influence the required foam quality. Consider both stability and mobility aspects.
Bonus: What adjustments could you make to the foam formulation to ensure optimal performance in this challenging environment?
Exercice Correction
The low permeability of the tight gas reservoir presents a challenge for foam mobility. To ensure the foam penetrates the tight formations, a **lower quality foam with a smaller gas fraction** is generally preferred. This will result in higher mobility, allowing the foam to flow through the narrow pore spaces. However, the high pressure environment poses a risk for foam stability. To overcome this, a higher quality foam with a larger gas fraction might be necessary. This will increase the foam's resistance to pressure changes and maintain its integrity within the reservoir. Therefore, finding a balance between mobility and stability is crucial. This might involve: * **Adjusting the surfactant concentration:** A higher surfactant concentration can improve foam stability but may decrease mobility. * **Selecting a suitable gas type:** Nitrogen typically offers better stability than CO2, which might be more appropriate for this high-pressure environment. * **Introducing a foam stabilizer:** Specific additives can further enhance foam stability under challenging conditions. By carefully considering these factors and adjusting the foam formulation accordingly, you can achieve optimal performance in this tight gas reservoir.
Books
- "Enhanced Oil Recovery: An Engineering Approach" by A.S. Abou-Kassem and M.J. Economides. (This book provides a comprehensive overview of EOR techniques, including foam flooding.)
- "Surfactants and Interfacial Phenomena" by Mysels, Shinoda, and Frankel. (Covers the fundamental principles of surfactants and their role in foam formation.)
- "Petroleum Engineering Handbook" by Tarek Ahmed. (Provides an overview of petroleum production and well stimulation techniques, including foam flooding.)
- "Foam Flooding: Fundamentals and Applications" by K.S. Sorbie. (This book focuses specifically on foam flooding, covering aspects like foam generation, propagation, and stability.)
Articles
- "Foam Stability and Its Effect on Oil Recovery" by S.L. Grifiths et al. in SPE Journal, 2003.
- "Foam Generation and Propagation in Porous Media" by J.J. Sheng et al. in SPE Journal, 1998.
- "Effect of Surfactant Concentration and Gas Type on Foam Quality and Mobility" by P.D. Rossen et al. in Journal of Petroleum Technology, 2000.
- "Measurement of Foam Quality and Its Application in Oil Recovery" by M.J. Economides et al. in Journal of Canadian Petroleum Technology, 1990.
Online Resources
- SPE (Society of Petroleum Engineers): https://www.spe.org - SPE is a professional society for petroleum engineers and offers a wealth of resources, including research papers, technical presentations, and conferences on foam flooding and EOR.
- Schlumberger: https://www.slb.com/ - Schlumberger is a leading oilfield services company that provides various technologies related to foam flooding. Their website offers technical information and case studies.
- Halliburton: https://www.halliburton.com/ - Halliburton is another major oilfield services company with extensive expertise in foam flooding. Their website provides information on their products and services.
- National Energy Technology Laboratory (NETL): https://www.netl.doe.gov/ - NETL is a research and development laboratory funded by the U.S. Department of Energy. They conduct research on various EOR technologies, including foam flooding.
Search Tips
- Use specific keywords like "foam quality," "foam flooding," "foam stimulation," "EOR," "surfactant," "gas injection," and "reservoir engineering."
- Combine keywords with terms like "measurement," "factors," "effect," "performance," and "optimization."
- Include the name of specific companies like "Schlumberger," "Halliburton," or "Baker Hughes" to find relevant resources.
- Utilize quotation marks around specific phrases to find exact matches.
- Explore academic databases like Scopus, Web of Science, and Google Scholar for research papers and technical publications.
Techniques
Chapter 1: Techniques for Measuring Foam Quality
This chapter will delve into the specific methods used to measure foam quality, providing a comprehensive overview of the available techniques.
1.1 Visual Inspection
- This is a simple and straightforward technique, primarily used for initial estimations.
- It involves visually observing the foam and judging the proportion of gas to liquid phases.
- This method is subjective and prone to errors, particularly at high gas fractions.
- It is often used in conjunction with other methods for a more accurate assessment.
1.2 Pressure Drop Measurement
- This method relies on measuring the pressure drop across a foam column.
- The principle is that a higher quality foam, with a greater gas fraction, will exhibit a higher resistance to flow, leading to a larger pressure drop.
- This technique is particularly useful for assessing foam stability under pressure changes.
1.3 Specialized Equipment
- This category encompasses a wide array of instruments specifically designed for measuring foam quality.
- Examples include:
- Foam Quality Meters: These devices use advanced sensors and algorithms to analyze foam characteristics and provide precise quality measurements.
- Foam Analyzer: These instruments use techniques such as optical imaging or laser scattering to determine the foam structure and gas fraction.
- Microscopic Analysis: Utilizing microscopes to observe the foam structure and quantify the gas phase content.
- These methods offer greater accuracy and reliability compared to visual inspection or pressure drop measurements.
1.4 Considerations for Selecting a Technique
- Application: The specific purpose of measuring foam quality will dictate the appropriate technique.
- Accuracy: The required level of precision will influence the choice of method.
- Cost: The budget available for equipment and testing will be a factor.
- Environment: The conditions in which the measurement is to be conducted (e.g., laboratory, field) may limit the available options.
1.5 Conclusion
Understanding the various techniques for measuring foam quality is crucial for optimizing its performance in oil and gas applications. Each method has its own advantages and limitations, and selecting the most suitable approach depends on the specific requirements of the application. By employing appropriate measurement techniques, operators can ensure that the foam is effectively utilized to enhance reservoir sweep efficiency and improve production efficiency.
Chapter 2: Models for Predicting Foam Quality
This chapter focuses on the theoretical models used to predict foam quality under various conditions.
2.1 Theoretical Models
- Foam quality is a complex phenomenon influenced by multiple factors, making its prediction challenging.
- Various theoretical models have been developed to predict foam quality based on fundamental principles and empirical relationships.
- These models typically incorporate parameters such as surfactant concentration, gas type, pressure, temperature, and reservoir properties.
2.2 Examples of Foam Quality Models
- Bikerman's Model: This model relates foam quality to the surface tension of the surfactant solution and the gas pressure.
- Katz and Hill Model: This model incorporates the effect of surfactant concentration and gas flow rate on foam quality.
- Hinch and Acrivos Model: This model considers the influence of surfactant concentration and the liquid viscosity on foam stability.
- Liu and Ruth Model: This model incorporates the effects of both gas and liquid flow rates on foam quality.
2.3 Limitations of Models
- Simplifications: Models often make simplifying assumptions to facilitate mathematical analysis, potentially leading to inaccuracies.
- Limited Applicability: Some models are only valid for specific conditions and may not be applicable to all reservoirs.
- Data Requirements: Accurate model predictions require reliable input data for relevant parameters.
2.4 Applications of Foam Quality Models
- Foam Design: Models can assist in designing foam fluids with desired quality characteristics for specific reservoir conditions.
- Reservoir Simulation: Foam quality models can be incorporated into reservoir simulations to predict foam movement and performance.
- Optimization: Models can help identify the optimal conditions for maximizing foam quality and production efficiency.
2.5 Conclusion
Theoretical models provide valuable tools for understanding and predicting foam quality. While they have limitations, they offer valuable insights into the factors influencing foam stability and performance. By utilizing models in conjunction with experimental data, operators can gain a comprehensive understanding of foam behavior and optimize its application in oil and gas production.
Chapter 3: Software for Foam Stimulation and Quality Analysis
This chapter explores the software tools available for simulating and analyzing foam stimulation processes and foam quality.
3.1 Simulation Software
- Reservoir Simulators: These software packages incorporate foam models to simulate the movement and performance of foam within a reservoir.
- Commercial Software: Many commercial reservoir simulation software packages offer foam modeling capabilities, including:
- CMG (Computer Modelling Group)
- Eclipse (Schlumberger)
- STARS (Reservoir Simulation)
- Open-Source Software: Open-source software packages, such as:
3.2 Capabilities of Foam Simulation Software
- Foam Generation: Simulate the formation of foam from injected fluids.
- Foam Transport: Track the movement and distribution of foam within the reservoir.
- Foam Properties: Account for the effects of foam quality, stability, and mobility on flow characteristics.
- Production Optimization: Evaluate the impact of foam stimulation on oil and gas production rates.
3.3 Foam Quality Analysis Software
- Specialized Tools: Several software programs are specifically designed for analyzing foam quality data obtained from laboratory experiments or field measurements.
- Data Processing: These tools can process and analyze large datasets to extract key foam parameters, such as quality, stability, and rheological properties.
- Visualization: Some software packages offer visualization tools to display foam quality results in a clear and informative manner.
3.4 Benefits of Using Software
- Improved Understanding: Simulation and analysis software provide a deeper understanding of foam behavior in complex reservoir environments.
- Optimized Design: Software tools can assist in optimizing foam fluid design and injection parameters for improved performance.
- Reduced Risk: Simulation can help assess the potential risks and benefits of foam stimulation before actual field implementation.
3.5 Conclusion
Software tools are indispensable for simulating and analyzing foam stimulation processes and foam quality. Utilizing these programs allows operators to optimize foam performance, improve production efficiency, and minimize risk associated with foam applications. By leveraging the capabilities of simulation and analysis software, operators can effectively manage foam stimulation strategies and maximize oil and gas recovery.
Chapter 4: Best Practices for Foam Stimulation and Quality Control
This chapter outlines the best practices for implementing foam stimulation and ensuring optimal foam quality throughout the process.
4.1 Foam Fluid Selection and Design
- Reservoir Characterization: Thoroughly understanding the reservoir properties, such as permeability, porosity, and pressure, is crucial for selecting the most suitable foam fluid.
- Surfactant Choice: Selecting the appropriate surfactant type and concentration is critical for achieving desired foam quality and stability under reservoir conditions.
- Gas Selection: The type of gas (e.g., nitrogen, CO2) used in the foam should be chosen based on its compatibility with the surfactant and the specific reservoir characteristics.
- Foam Quality Testing: Laboratory testing is essential to verify the foam quality and stability under simulated reservoir conditions.
4.2 Foam Injection and Monitoring
- Injection Rate and Pressure: Carefully controlling the injection rate and pressure of the foam fluid is crucial for maintaining desired foam quality and distribution within the reservoir.
- Monitoring and Optimization: Continuous monitoring of foam injection parameters and production data allows for adjustments and optimization to maintain optimal foam performance.
- Data Analysis: Regular analysis of production data, pressure profiles, and fluid samples provides insights into the effectiveness of foam stimulation and helps identify any issues with foam quality.
4.3 Quality Control Measures
- Regular Testing: Periodic testing of foam fluid samples at the wellhead or during production can help ensure that the foam is maintaining desired quality.
- Foam Quality Monitoring: Using downhole sensors or specialized tools to monitor foam quality in real-time can provide valuable information for optimizing injection parameters.
- Quality Control Procedures: Implementing strict quality control procedures throughout the foam stimulation process can help minimize variations in foam quality and ensure optimal performance.
4.4 Conclusion
Following best practices for foam stimulation and implementing rigorous quality control measures are crucial for maximizing the effectiveness of foam applications in oil and gas production. By carefully selecting and designing foam fluids, controlling injection parameters, and monitoring foam quality throughout the process, operators can ensure that foam stimulation is implemented successfully and achieves desired results.
Chapter 5: Case Studies of Foam Stimulation and Quality Control
This chapter provides real-world examples of foam stimulation applications and highlights the importance of foam quality in achieving successful production enhancements.
5.1 Case Study 1: Improved Oil Recovery in a Mature Field
- Challenge: A mature oil field with declining production rates.
- Solution: Foam stimulation was implemented to improve sweep efficiency and increase oil recovery.
- Results: Significant increase in oil production rates, demonstrating the effectiveness of foam stimulation in revitalizing aging fields.
- Key Takeaway: Optimal foam quality was essential for achieving the desired results in this case study.
5.2 Case Study 2: Gas Production Optimization in a Tight Gas Reservoir
- Challenge: Low production rates in a tight gas reservoir due to limited permeability.
- Solution: Foam stimulation was used to improve gas mobility and increase production.
- Results: A substantial increase in gas production rates, indicating the success of foam stimulation in enhancing gas flow in low-permeability formations.
- Key Takeaway: Carefully controlled foam quality was crucial for optimizing gas production in this tight reservoir.
5.3 Case Study 3: Foam Stimulation in a Fractured Reservoir
- Challenge: A complex fractured reservoir with heterogeneous permeability.
- Solution: Foam stimulation was implemented to improve sweep efficiency and reduce water production.
- Results: Significant reduction in water production and improved oil recovery, demonstrating the adaptability of foam stimulation to complex reservoir systems.
- Key Takeaway: Monitoring foam quality and adjusting injection parameters were essential for achieving desired results in this fractured reservoir.
5.4 Conclusion
These case studies illustrate the diverse applications of foam stimulation in oil and gas production and emphasize the crucial role of foam quality in achieving desired results. By carefully controlling foam quality and implementing best practices throughout the process, operators can successfully utilize foam stimulation technologies to improve production efficiency and maximize oil and gas recovery.
Comments