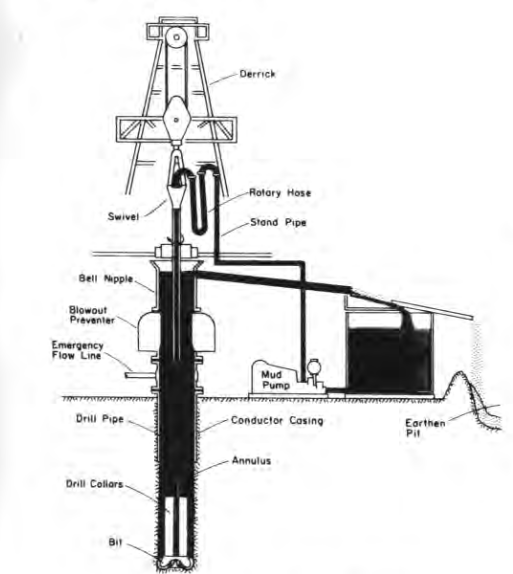
قلب استكشاف النفط والغاز: نظرة على منصات الحفر
تُعد منصات الحفر العمود الفقري لصناعة النفط والغاز، فهي تُمثل المنصة الأساسية لاستكشاف واستخراج هذه الموارد الثمينة. تُعدّ هذه الآلات المعقدة مسؤولة عن الحفر في الأرض واستخراج الهيدروكربونات وإعداد البئر للإنتاج.
تتناول هذه المقالة المكونات الرئيسية لمنصة الحفر، مع التركيز على المعدات السطحية التي تُشغل عملية الحفر.
رفع وخفض سلسلة الحفر:
سلسلة الحفر، وهي تجميع معقد من أنابيب الحفر، وعنق الحفر، ومثقاب الحفر، تُعدّ الوصلة لنقل سائل الحفر وتدوير المثقاب. لإدارة هذا المكون الحيوي، تستخدم منصات الحفر المعدات التالية:
- البرج: هذا الهيكل المرتفع، المصنوع غالبًا من الفولاذ، يُوفر إطارًا لرفع وخفض سلسلة الحفر، بالإضافة إلى معدات ثقيلة أخرى.
- آلة السحب: قلب المنصة، آلة السحب هي نظام رافعة قوي يُرفع ويخفض سلسلة الحفر.
- نظام الرفع: يتكون هذا النظام من آلة السحب، وعجلة القمة، وعجلة التنقل، ويُدير وزن سلسلة الحفر ويُسهّل تحركها لأعلى ولأسفل من بئر النفط.
- طاولة الدوران: هذه المنصة الدوارة تُتصل بقمة سلسلة الحفر، وتُوفر القوة اللازمة لتدوير مثقاب الحفر.
- محرك الدفع العلوي: بديل لطاولة الدوران، يسمح محرك الدفع العلوي بسرعات حفر أسرع وتحكم أكبر في سلسلة الحفر.
تدوير مثقاب الحفر وتداول سائل الحفر:
تتطلب عملية الحفر دورانًا مستمرًا لمثقاب الحفر وتدفقًا ثابتًا لسائل الحفر لأسفل سلسلة الحفر. يتم تحقيق ذلك بواسطة:
- مضخات الطين: تدفع هذه المضخات القوية سائل الحفر لأسفل السلسلة، مما يُشحّم المثقاب، ويُزيل القطع، ويُحافظ على استقرار بئر النفط.
- نظام الطين: يتضمن هذا النظام الشامل مكونات مختلفة مثل خزانات الطين، ومهزازات الطين، والطرد المركزي، مسؤولة عن تحضير وتداول وتنظيف سائل الحفر.
- نظام الطاقة: تتطلب منصة الحفر مصدر طاقة موثوق به لتشغيل مكوناتها العديدة. يمكن توفير ذلك بواسطة محركات الديزل، أو التوربينات الغازية، أو الاتصالات الكهربائية.
اعتبارات رئيسية في عمليات منصة الحفر:
- السلامة: تُعد عمليات منصة الحفر خطرة بطبيعتها، وتتطلب تركيزًا دقيقًا على بروتوكولات السلامة والإجراءات.
- الكفاءة: تُعد عمليات الحفر المُحسنة ضرورية لزيادة استخراج الموارد وتقليل التكاليف.
- البيئة: تركز الصناعة بشكل متزايد على تقليل التأثير البيئي لعمليات الحفر، باستخدام ممارسات وتقنيات مستدامة.
الخلاصة:
تُعد منصة الحفر شهادة على براعة الإنسان وتعقيد استخراج النفط والغاز. تُمكن معداتها وعملياتها المتطورة من استكشاف وتطوير هذه المصادر الحيوية للطاقة، مع طرح تحديات كبيرة في مجال السلامة والكفاءة والتأثير البيئي. مع تطور التكنولوجيا، ستستمر منصة الحفر بالتأكيد في التكيف، ودفع حدود استكشاف وإنتاج النفط والغاز.
Test Your Knowledge
Drilling Rig Quiz
Instructions: Choose the best answer for each question.
1. What is the primary function of a drilling rig? a) To transport oil and gas to refineries. b) To explore and extract oil and gas from the earth. c) To refine oil and gas into usable products. d) To store and distribute oil and gas.
Answer
b) To explore and extract oil and gas from the earth.
2. Which of the following components is NOT directly involved in lifting and lowering the drilling string? a) Derrick b) Drawworks c) Rotary Table d) Hoisting System
Answer
c) Rotary Table
3. What is the purpose of drilling fluid? a) To lubricate the drill bit and remove cuttings. b) To provide power to the rotary table. c) To store oil and gas extracted from the well. d) To regulate the flow of oil and gas.
Answer
a) To lubricate the drill bit and remove cuttings.
4. Which of the following is NOT a key consideration in drilling rig operations? a) Safety b) Efficiency c) Environmental impact d) Cost of refining oil and gas
Answer
d) Cost of refining oil and gas
5. What is the role of the mud pumps in the drilling process? a) To rotate the drill bit. b) To lift and lower the drilling string. c) To circulate drilling fluid down the drill string. d) To store drilling fluid.
Answer
c) To circulate drilling fluid down the drill string.
Drilling Rig Exercise
Scenario: You are the drilling supervisor on a new oil exploration project. Your team needs to drill a well 2,000 meters deep. The drilling string weighs 50 tons, and the drill bit needs to rotate at 100 RPM.
Task:
1. Outline the steps involved in the drilling process, from preparing the drilling string to reaching the target depth. 2. Briefly describe the roles of the following equipment in this process: * Derrick * Drawworks * Rotary Table * Mud Pumps * Mud System 3. What safety concerns should you address before and during drilling operations? 4. How would you ensure efficient drilling operations and minimize environmental impact?
Exercice Correction
**Steps involved in drilling:**
- Preparing the drilling string: Assemble the drill string, including the drill pipe, drill collars, and drill bit, ensuring proper connections.
- Lifting and lowering the drilling string: Use the derrick and drawworks to lower the drilling string into the wellbore.
- Rotating the drill bit: Engage the rotary table to rotate the drill bit at the desired speed (100 RPM) while circulating drilling fluid.
- Drilling and cutting: The rotating drill bit cuts through the rock formations, creating a wellbore.
- Circulating drilling fluid: Mud pumps push drilling fluid down the drill string to lubricate the bit, remove cuttings, and maintain wellbore stability.
- Monitoring drilling progress: Track drilling depth, rate of penetration, and other parameters.
- Reaching the target depth: Continue drilling until the target depth (2,000 meters) is reached.
- Casing and cementing: Run casing into the wellbore and cement it to stabilize the wellbore and prevent fluid leaks.
Equipment roles:
- Derrick: Provides a framework for hoisting and lowering the drilling string, along with other heavy equipment.
- Drawworks: Raises and lowers the drilling string, controlling the weight and tension on the drill string.
- Rotary Table: Rotates the drill string, providing power to the drill bit.
- Mud Pumps: Circulate drilling fluid down the drill string and back to the surface.
- Mud System: Prepares, circulates, and cleans drilling fluid.
Safety Concerns:
- Rig setup and inspection: Ensure the rig is properly assembled, inspected, and in good working condition.
- Personnel training: Make sure all personnel are trained in safe drilling procedures.
- Emergency procedures: Establish clear emergency response plans and communication protocols.
- Well control: Implement well control measures to prevent blowouts and other incidents.
- Working at heights: Provide safety equipment and training for workers operating at height.
- Heavy lifting: Ensure proper procedures and equipment for handling heavy loads.
Efficiency and Environmental Impact:
- Optimized drilling parameters: Adjust drilling parameters like bit weight and rotation speed for optimal performance.
- Wellbore stability: Use appropriate drilling fluid to maintain wellbore stability and prevent wellbore collapse.
- Minimizing waste: Recycle drilling fluid and cuttings, minimize emissions from drilling operations, and comply with environmental regulations.
- Sustainable practices: Consider adopting environmentally friendly drilling technologies and practices.
Books
- Drilling Engineering: Principles and Practices by M.P. Sharma & K.S. Rao: Provides a comprehensive overview of drilling engineering principles and practices, including drilling rigs and their components.
- Petroleum Engineering: Drilling and Well Completion by B.H. Lathi: A classic textbook covering all aspects of drilling, including a detailed explanation of drilling rigs and their operations.
- The Complete Guide to Oil and Gas Exploration and Production by Michael T. Economides & John H. Nolte: Offers a broad understanding of the oil and gas industry, including a chapter on drilling rigs and their role in exploration and production.
- Drilling and Well Service Engineering by R.A. Dean & R.B. Nicholson: Focuses on the engineering aspects of drilling and well services, with significant attention to drilling rigs and their equipment.
Articles
- "Drilling Rigs: The Backbone of Oil and Gas Exploration" by [Your Name]: This article you provided could be a great starting point, with its detailed description of drilling rig components.
- "A Comprehensive Review of Drilling Rig Design and Operation" by [Author(s)]: Search for recent journal articles published in engineering and petroleum journals.
- "The Evolution of Drilling Rigs: From Early Designs to Modern Technology" by [Author(s)]: Find articles exploring the history and technological advancements of drilling rigs.
Online Resources
- SPE (Society of Petroleum Engineers): https://www.spe.org/ Offers numerous resources including journal articles, conferences, and technical papers related to drilling rigs.
- Oil & Gas Journal: https://www.ogj.com/ Provides industry news, articles, and technical information covering drilling rigs and other oil and gas technologies.
- DrillingInfo: https://www.drillinginfo.com/ Offers comprehensive data and analytics related to drilling activity, including rig counts, performance metrics, and drilling technology.
- Offshore Technology: https://www.offshore-technology.com/ Covers the latest news, projects, and technologies in offshore oil and gas exploration, including drilling rigs designed for offshore operations.
Search Tips
- Use specific keywords: "Drilling rig components", "types of drilling rigs", "drilling rig operations", "drilling rig safety", "drilling rig technology".
- Combine keywords with specific terms: "Drilling rig design + safety standards", "drilling rig maintenance + best practices", "drilling rig technology + environmental impact".
- Use quotation marks: "drilling rig" + "rotary table" will find pages containing both terms together.
- Filter by date and source: Use filters to narrow down your results by specific dates, websites, or file types.
- Use advanced search operators: "site:spe.org drilling rigs" to search for specific keywords on a particular website.
Techniques
Drilling Rig: A Comprehensive Overview
Here's a breakdown of the provided text into separate chapters, expanding on the information to create a more comprehensive overview:
Chapter 1: Techniques
Drilling Techniques Employed in Modern Drilling Rigs
Drilling techniques employed on a rig are crucial for efficient and safe hydrocarbon extraction. The choice of technique depends on factors like the geological formation, well depth, and the type of hydrocarbon being targeted. Key techniques include:
- Rotary Drilling: This is the most common method, using a rotating drill bit to cut through rock formations. It utilizes the drawworks, top drive, and rotary table described in the initial text to rotate the drill string. Different bit types (roller cone, PDC) are selected based on the formation's hardness.
- Directional Drilling: This technique allows for the deviation of the wellbore from its vertical path, enabling access to multiple reservoirs from a single surface location. This involves using specialized tools like bent sub assemblies and mud motors to steer the drill bit.
- Horizontal Drilling: A specialized form of directional drilling, where the wellbore is drilled horizontally to access extended reservoir sections, maximizing production. This technique is particularly useful in shale gas and tight oil formations.
- Underbalanced Drilling: This technique maintains a lower pressure in the wellbore than the formation pressure. It minimizes formation damage and improves drilling efficiency in certain conditions, but requires careful management to prevent well control issues.
- Managed Pressure Drilling (MPD): A sophisticated technique that precisely controls pressure throughout the wellbore, enhancing safety and efficiency. It’s particularly useful in challenging wells prone to pressure surges or losses.
Advances in drilling techniques continuously push the boundaries of exploration, allowing access to previously unreachable resources and improving the overall efficiency and safety of drilling operations.
Chapter 2: Models
Drilling Rig Models: A Spectrum of Capabilities
Drilling rigs are categorized into various models based on their capacity, mobility, and application. The choice of rig model depends heavily on the specific drilling project's requirements.
- Land Rigs: These are stationary rigs used for onshore drilling. They vary significantly in size and capacity, from smaller rigs for shallow wells to massive rigs for deepwater exploration.
- Offshore Rigs: Designed for marine environments, offshore rigs are further subdivided into different types:
- Jack-up rigs: Supported by legs that rest on the seabed.
- Semi-submersible rigs: Float on pontoons and are partially submerged.
- Drill ships: Self-propelled vessels equipped with drilling equipment.
- Mobile Rigs: These rigs are designed for easy transportation and setup, often used for exploration in remote locations. They offer flexibility but might have lower capacity than larger land rigs.
Each rig model incorporates specific design features optimized for its intended environment and drilling operations. Factors like deck space, hoisting capacity, and mud system capabilities differ considerably between models.
Chapter 3: Software
Software Applications in Drilling Rig Operations
Modern drilling rigs heavily rely on software to optimize performance, enhance safety, and improve data management. Key software applications include:
- Drilling Automation Systems: These systems automate various drilling processes, improving efficiency and reducing human error. This can include automated pipe handling, mud pump control, and real-time monitoring of drilling parameters.
- Well Planning Software: Used to design and optimize well trajectories, predict formation properties, and manage drilling fluids. This ensures efficient drilling operations and minimizes potential risks.
- Data Acquisition and Management Systems: These systems collect and process vast amounts of data from various sensors on the rig. This data is then used for real-time monitoring, analysis, and reporting, facilitating decision-making.
- Reservoir Simulation Software: Helps to model reservoir behavior and predict production performance, assisting in optimizing well placement and completion strategies.
- Health, Safety, and Environment (HSE) Software: Helps manage safety protocols, track incidents, and ensure compliance with regulatory requirements.
The integration of these software applications is crucial for maximizing the efficiency, safety, and profitability of drilling operations.
Chapter 4: Best Practices
Best Practices for Safe and Efficient Drilling Rig Operations
Maintaining safety and maximizing efficiency are paramount in drilling rig operations. Best practices involve a multifaceted approach, encompassing:
- Rigorous Safety Protocols: Implementing stringent safety procedures, regular safety training for personnel, and proactive risk assessments are crucial to minimize accidents.
- Optimized Drilling Parameters: Careful selection of drilling parameters (weight on bit, rotary speed, mud properties) is critical for maintaining optimal drilling rate while minimizing equipment wear and formation damage.
- Preventive Maintenance: Regular maintenance of rig equipment is essential for preventing breakdowns and ensuring reliable operation. This includes both routine inspections and scheduled overhauls.
- Data-Driven Decision Making: Utilizing real-time data from sensors and software applications to monitor drilling parameters and make informed decisions in real-time.
- Environmental Stewardship: Minimizing the environmental impact of drilling operations by employing sustainable practices, such as waste management and efficient fluid handling, is crucial for responsible operations.
- Effective Communication: Clear and concise communication between rig crew members is essential for coordination and safety. This involves using standardized procedures and communication tools.
Adhering to these best practices is essential for achieving a balance between safety, efficiency, and environmental responsibility.
Chapter 5: Case Studies
Drilling Rig Case Studies: Demonstrating Best Practices and Challenges
(This section would require specific examples. Here's a framework for how case studies could be structured):
Case Study 1: Successful Application of Managed Pressure Drilling in a High-Pressure, High-Temperature Well
- Description of the well and its challenges.
- Implementation of MPD and its impact on safety and efficiency.
- Lessons learned and best practices demonstrated.
Case Study 2: Environmental Mitigation Strategies in an Offshore Drilling Project
- Environmental challenges posed by the project location.
- Implementation of environmental protection measures.
- Assessment of environmental impact and successful mitigation strategies.
Case Study 3: Improving Drilling Efficiency through Advanced Automation
- Description of the automation systems implemented.
- Quantitative results demonstrating increased drilling efficiency.
- Analysis of the cost-benefit of the automation investment.
These case studies would showcase successful implementations of best practices and highlight the challenges and lessons learned in different drilling scenarios.
This expanded structure provides a more detailed and organized overview of drilling rigs, encompassing various aspects from techniques and models to software and best practices, concluding with illustrative case studies. Remember to replace the placeholder content in the Case Studies chapter with real-world examples.
Comments